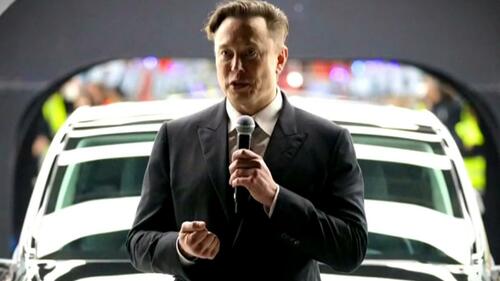
When most analysts discuss Tesla, they focus on new vehicles or the electric vehicle company’s advancements in autonomy. Yet, according to Launch i/o CEO Jeff Lutz, one of the most significant—and under-discussed—developments at Tesla is happening not in its design studios or on the road, but in its factories. Lutz, a former executive at Google and Motorola, argues that Tesla’s true innovation isn’t just the electric vehicles or robots it’s building, but how those products are being made. The company’s first-principles approach to manufacturing is a radical departure from the industry norm, focusing not just on cheap labor or existing models, but on rethinking the entire production process.
Tesla is creating factories that are the product—designing, testing, and perfecting every element just as they do with their cars. This focus on manufacturing efficiency, Lutz believes, will lead to a dramatic reduction in production costs, potentially bringing them closer to zero. And this shift in how products are built—rather than merely assembled—could set a new standard for the entire manufacturing world.
.@thejefflutz to @farzyness: Tesla is Revolutionizing Manufacturing—And Few Are Talking About It
— CAPITAL (@capitalnewshq) December 25, 2024
"The most under-discussed thing in the analyst world about Tesla is not the new vehicles coming, nor the growing discussions about autonomy, but rather Tesla's next product: their… pic.twitter.com/a5a60vBxJR
FARZAD MESBAHI: It's no wonder that innovation has been lacking so much it's because we've brute forced essentially manufacturing by leveraging globalization because we had that $2 an hour rate in China or Mexico wherever else like we're not like well we have to just get really good at building stuff to be competitive I was like nah just let him do it like we'll get get our margins just let them do it.
JEFF LUTZ: The most under-discussed thing in the analyst world about Tesla is not the new vehicles coming, nor the growing discussions about autonomy, but rather Tesla's next product: their new way of manufacturing. It's a big deal, a huge step in how products are made today, and I don't think many investment firms have the right research people actually looking into what this impact is and what it's going to enable. It's going to enable the variable cost to build products to shrink further and further, approaching zero.
This is the step function needed for cost reduction to achieve further scale, and I don’t think enough people are talking about it. It’s going to be how the Cybertruck is made, how Optimus will be made. Tesla versions its factories like they version their product. They spend time perfecting it and have design reviews of their factory designs just as they do with their products. They have specs and performance attributes they are trying to meet. This is very different from what happens at other companies at the executive level.
FARZAD MESBAHI: This is such a profound statement because a lot of the stories that I hear are related to, like, say Tesla capitalizing on making manufacturing the product—really just honing in so much on the factory that it becomes the product, the you know, and where we throw around 2 million cars per year, five million cars per year per factory, tens of millions of bots per year sooner than people think. The usual narrative is crazy, pie-in-the-sky; they can't do that, look at Ford, look at BYD, they can only do so much.
But what we're missing here is that we've had decades of just sitting on our asses, leveraging cheaper labor versus going out of our way to really push the boundaries of engineering and manufacturing. And now that we have a company that's willing to do that because the leader is viewing that as a first principles approach to manufacturing, right? Instead of like, okay, cheap labor is good, but why aren’t we pushing manufacturing and engineering as much as we can to make this as efficient and as productive as possible?
Of course they’re extremely talented, they’re doing something very unique, but it’s also on the backs of 30-40 years of, I’m going to call it laziness. Like, you're just taking the easy way out, and I get it, more profits, you're taking care of shareholders—I get it—but you're not really pushing the boundaries of manufacturing. I think what this leads to is, if companies and leaders truly take this to heart, we’re going to see an explosion in manufacturing across the board. It’s not just going to be a Tesla thing; I think we’re going to see it all over the place.
JEFF LUTZ: I’m advising companies on this now, you're going to see massive localization of manufacturing. People think costs just instantly go up when you do that. They do unmitigated, but if you're a company like Tesla and you're thinking about it the way they do, they're actually focused on localizing and making costs go down. Think of it, how many auto factories are expanding in Germany? Just answer that question.
Watch the entire exchange here:
When most analysts discuss Tesla, they focus on new vehicles or the electric vehicle company’s advancements in autonomy. Yet, according to Launch i/o CEO Jeff Lutz, one of the most significant—and under-discussed—developments at Tesla is happening not in its design studios or on the road, but in its factories. Lutz, a former executive at Google and Motorola, argues that Tesla’s true innovation isn’t just the electric vehicles or robots it’s building, but how those products are being made. The company’s first-principles approach to manufacturing is a radical departure from the industry norm, focusing not just on cheap labor or existing models, but on rethinking the entire production process.
Tesla is creating factories that are the product—designing, testing, and perfecting every element just as they do with their cars. This focus on manufacturing efficiency, Lutz believes, will lead to a dramatic reduction in production costs, potentially bringing them closer to zero. And this shift in how products are built—rather than merely assembled—could set a new standard for the entire manufacturing world.
.@thejefflutz to @farzyness: Tesla is Revolutionizing Manufacturing—And Few Are Talking About It
“The most under-discussed thing in the analyst world about Tesla is not the new vehicles coming, nor the growing discussions about autonomy, but rather Tesla’s next product: their… pic.twitter.com/a5a60vBxJR
— CAPITAL (@capitalnewshq) December 25, 2024
FARZAD MESBAHI: It’s no wonder that innovation has been lacking so much it’s because we’ve brute forced essentially manufacturing by leveraging globalization because we had that $2 an hour rate in China or Mexico wherever else like we’re not like well we have to just get really good at building stuff to be competitive I was like nah just let him do it like we’ll get get our margins just let them do it.
JEFF LUTZ: The most under-discussed thing in the analyst world about Tesla is not the new vehicles coming, nor the growing discussions about autonomy, but rather Tesla’s next product: their new way of manufacturing. It’s a big deal, a huge step in how products are made today, and I don’t think many investment firms have the right research people actually looking into what this impact is and what it’s going to enable. It’s going to enable the variable cost to build products to shrink further and further, approaching zero.
This is the step function needed for cost reduction to achieve further scale, and I don’t think enough people are talking about it. It’s going to be how the Cybertruck is made, how Optimus will be made. Tesla versions its factories like they version their product. They spend time perfecting it and have design reviews of their factory designs just as they do with their products. They have specs and performance attributes they are trying to meet. This is very different from what happens at other companies at the executive level.
FARZAD MESBAHI: This is such a profound statement because a lot of the stories that I hear are related to, like, say Tesla capitalizing on making manufacturing the product—really just honing in so much on the factory that it becomes the product, the you know, and where we throw around 2 million cars per year, five million cars per year per factory, tens of millions of bots per year sooner than people think. The usual narrative is crazy, pie-in-the-sky; they can’t do that, look at Ford, look at BYD, they can only do so much.
But what we’re missing here is that we’ve had decades of just sitting on our asses, leveraging cheaper labor versus going out of our way to really push the boundaries of engineering and manufacturing. And now that we have a company that’s willing to do that because the leader is viewing that as a first principles approach to manufacturing, right? Instead of like, okay, cheap labor is good, but why aren’t we pushing manufacturing and engineering as much as we can to make this as efficient and as productive as possible?
Of course they’re extremely talented, they’re doing something very unique, but it’s also on the backs of 30-40 years of, I’m going to call it laziness. Like, you’re just taking the easy way out, and I get it, more profits, you’re taking care of shareholders—I get it—but you’re not really pushing the boundaries of manufacturing. I think what this leads to is, if companies and leaders truly take this to heart, we’re going to see an explosion in manufacturing across the board. It’s not just going to be a Tesla thing; I think we’re going to see it all over the place.
JEFF LUTZ: I’m advising companies on this now, you’re going to see massive localization of manufacturing. People think costs just instantly go up when you do that. They do unmitigated, but if you’re a company like Tesla and you’re thinking about it the way they do, they’re actually focused on localizing and making costs go down. Think of it, how many auto factories are expanding in Germany? Just answer that question.
Watch the entire exchange here:
[embedded content]
Loading…