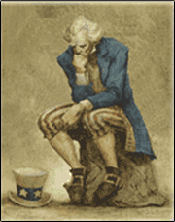
(function(d, s, id) { var js, fjs = d.getElementsByTagName(s)[0]; if (d.getElementById(id)) return; js = d.createElement(s); js.id = id; js.src = “https://connect.facebook.net/en_US/sdk.js#xfbml=1&version=v3.0”; fjs.parentNode.insertBefore(js, fjs); }(document, ‘script’, ‘facebook-jssdk’)); –>
–>
February 5, 2024
The American economy can’t catch a break. In addition to the massive price inflation of food, cars, housing, energy, and so many other elements, international companies are now suffering from a near-doubling of ocean transportation costs in just the past three months, due to simultaneous crises in Central America and the Red Sea that have restricted international shipping through the Panama and Suez Canals.
‘); googletag.cmd.push(function () { googletag.display(‘div-gpt-ad-1609268089992-0’); }); document.write(”); googletag.cmd.push(function() { googletag.pubads().addEventListener(‘slotRenderEnded’, function(event) { if (event.slot.getSlotElementId() == “div-hre-Americanthinker—New-3028”) { googletag.display(“div-hre-Americanthinker—New-3028”); } }); }); }
This is adding to the cost of goods all over the world, along with damaging lead times, as longer transits cause disruptions to both factory schedules and retail offerings.
For thousands of years, ocean carriers moved cargo. They would fill up a ship with drums, barrels, crates, and boxes of goods. Their math was relatively straightforward: charge for the transportation of the goods based on how much it cost to make the trip from port to port.
In the mid 20th century, Malcom McLean introduced a cost-effective way to switch most of the ocean industry to intermodal container shipping. This means that most ships are now configured to transport thousands of stacked containers each in standard sizes — mostly 20’ and 40’ long — measured in “twenty foot equivalent units” or TEUs. So, for example, a ship that holds 1750 standard or highcube 40’ containers is referred to as a 3500 TEU vessel.
‘); googletag.cmd.push(function () { googletag.display(‘div-gpt-ad-1609270365559-0’); }); document.write(”); googletag.cmd.push(function() { googletag.pubads().addEventListener(‘slotRenderEnded’, function(event) { if (event.slot.getSlotElementId() == “div-hre-Americanthinker—New-3035”) { googletag.display(“div-hre-Americanthinker—New-3035”); } }); }); }
There are now thousands of such ships on the high seas every day, traversing weekly scheduled routes, quickly transporting hundreds or even thousands of these reusable cargo containers. Huge cranes swing each container off the ship and onto a waiting rail car. At rail hubs hundreds of miles inland, another crane swings each container off the train and onto a truck waiting with a specialized chassis for the final delivery to a warehouse or factory.
The shipping lines have had to switch thought processes. They no longer move freight, as such; they now rent out these containers. That means they have to anticipate how many empty containers they will need each week at points of origin, so they can handle the cargo booked for them. Since there’s never an exact match of imported cargo and exported cargo, the carriers move hundreds of thousands of empty containers all the time. It’s a cost of doing business.
This process has been honed to a fine point over the past 70 years, and worked wonderfully until the painful market disruptions of the COVID “pandemic,” when massive bottlenecks caused by understaffing at seaports, railroad hubs, and warehouses due to “social distancing” doubled and even trebled transit times.
Now we are seeing similar problems with two completely different causes.
The global shipping community has become dependent on the Panama Canal. An immense amount of cargo — several dozen ships, holding from 1500 to 8000 forty-foot containers each — have crossed the Panama Canal every single day for decades.
But last fall, a combination of a severe drought in Central America, and the Panama government’s failure to properly plan for such a drought in their last huge expansion, has required Panama to greatly curtail the vessels using the canal.
‘); googletag.cmd.push(function () { googletag.display(‘div-gpt-ad-1609268078422-0’); }); document.write(”); googletag.cmd.push(function() { googletag.pubads().addEventListener(‘slotRenderEnded’, function(event) { if (event.slot.getSlotElementId() == “div-hre-Americanthinker—New-3027”) { googletag.display(“div-hre-Americanthinker—New-3027”); } }); }); } if (publir_show_ads) { document.write(“
Now Panama must limit the crossings to fewer than twenty vessels a day, and those twenty must be either on the small side, or, if large, must be loaded far below capacity, in order to handle the reduced drafts in the locks (there’s no longer enough water to float the heaviest ships). On top of this, Panama is hiking the prices for using the locks at all.
Shipping lines have to choose between taking the much longer route around South America or reducing their payload, leaving a third or half of their potential cargo unbooked so they can be one of the few using the canal at these higher prices. A lose-lose scenario.
As an example of how severe a choice this is, Maersk is taking the unprecedented step of deciding to unload their ships on one side of Panama and then rail the contents across the isthmus, reloading it all into another empty ship at the other side. Consider the cost of unlading thousands of containers, railing them, then positioning an empty ship to accept them all at the other end. The fact that this costly option is cost-effective by comparison should clarify how incredibly expensive the additional cost of sailing around South America is, now that we’ve had a century to become dependent upon the Panama Canal.
Half a world away, the situation is even worse.
Almost all transportation between Europe and Asia goes through the Suez Canal. The Iran-funded Houthi rebels, who have been attacking cargo ships in the Red Sea for months, have now effectively driven all the shipping lines out of the region. They don’t have any rail options like we do in the Americas; if you can’t get to Suez, you have to sail around Africa, or go around the world in the other direction and sail through Panama.
Now, it should be obvious what this does to global inflation: The lines are sailing half-empty ships, and having to buy hundreds of thousands of additional empty containers (almost all made in China). Transportation costs are increasing by 50% to 100% over just the past three months on almost everything moving by sea. We suffer lengthening of transit times in many major lanes, and considerable disruption of factory schedules as critical components are late.
But what public policy lessons can we draw from this?
- The United States chose to give up the Panama Canal during the Carter administration. With our rigorous processes for major capital projects, it’s inconceivable that a Panama Canal under U.S. control would have undergone its recent expansion without making proper provision for the necessary additional water sources to prepare for an extended drought.
- The Houthi rebels are controlled by Iran. They have been active in Yemen since the 1990s, but never caused significant trouble in the Red Sea until the fall of 2023, after the Biden-Harris regime broadly eased controls on Iran and authorized massive new funding sources to the mullahs of Tehran. The Houthis would have neither the weaponry nor the free hand to pursue such attacks were it not for the pro-Iranian moves and general foreign policy weaknesses of the Biden administration, which has seen the United States lose its hard-fought respect throughout the world.
- Global trade itself — the free flow of goods at market prices — is generally an economic and societal good, but not when a preponderance of domestic industry becomes dependent on it, especially on imports from a single source. Over the past 40 years, both the American and European economies have become dependent on mass imports from China. This is the reason why these current canal problems are a massive one-two punch to the global economy, rather than just a harmless hiccup.
What we teach in our business schools, how our manufacturers source the materials they make and sell, which business choices are rewarded or punished by Wall Street investors — and most of all, who we elect to public office — makes a difference. Sometimes a very costly difference indeed.
John F. Di Leo is a Chicagoland-based international transportation manager, trade compliance trainer and speaker. A one-time Milwaukee County Republican Party chairman, he has been writing a regular column for Illinois Review since 2009. Read his book on vote fraud (The Tales of Little Pavel) and his political satires on the current administration (Evening Soup with Basement Joe, Volumes I and II, and the recently released Volume Three).
Image: User Stan Shebs
<!–
–>
<!– if(page_width_onload <= 479) { document.write("
“); googletag.cmd.push(function() { googletag.display(‘div-gpt-ad-1345489840937-4’); }); } –> If you experience technical problems, please write to [email protected]
FOLLOW US ON
<!–
–>
<!– _qoptions={ qacct:”p-9bKF-NgTuSFM6″ }; –> <!—-> <!– var addthis_share = { email_template: “new_template” } –>